MONDAY 8 OCTOBER |
|
8:00 - 9:00 |
REGISTRATION |
9:00 - 13:00 |
PLENARY SESSION |
13:00 -14:00 |
Lunch Break Time |
14:00 - 18:00 |
AEROSPACE & DEFENCE |
14:00 - 18:00 |
AUTOMOTIVE (part 1) |
14:00 - 18:00 |
MATERIALS MODELLING |
14:00 - 18:00 |
SMART PRODUCTS & IoT |
14:00 - 18:00 |
SYSTEM LEVEL SIMULATION (part 1) |
14:00 - 18:00 |
SYSTEMS DYNAMICS |
14:00 - 18:00 |
TRANSPORTATION (part 1) |
14:00 - 17:00 |
Workshop | Co-design di componenti colati e forgiati | Come il dialogo con i fornitori può migliorare la qualità e le performance dei vostri prodotti |
14:00 - 18:00 |
Workshop | Exascale Computing Workshop: Experiences and Best Practices for Porting Applications to Emerging HPC Architectures and Platforms (part 1) |
14:00 - 18:00 |
BEST PRACTICES AREA |
18:00 |
Poster Award Ceremony |
TUESDAY 9 OCTOBER Morning |
|
8:00 - 9:00 |
REGISTRATION |
9:00 - 12:40 |
AUTOMOTIVE (part 2) |
9:00 - 12:40 |
CIVIL ENGINEERING (part 1) |
9:00 - 12:40 |
FOUNDRY |
9:00 - 12:40 |
OIL & GAS |
9:00 - 12:40 |
STEELMAKING & METAL DEFORMATION |
9:30 - 13:00 |
Workshop | Geometric Dimensioning and Tolerancing (GD&T) Workshop |
9:30 - 13:00 |
Tavola Rotonda | Industria 4.0: Valorizzare gli investimenti con competenze e tecnologie software di Industrial Analytics. Come utilizzare i dati per accrescere la competitività delle imprese 4.0 |
9:30 - 13:00 |
Workshop | Exascale Computing Workshop: Experiences and Best Practices for Porting Applications to Emerging HPC Architectures and Platforms (part 2) |
10:00 - 13:00 |
Workshop | Digital Twin, la nuova dimensione della simulazione numerica: un workshop interattivo e con una visione alto manageriale delle logiche di business derivanti (part 1) |
10:00 - 13:00 |
BEST PRACTICES AREA |
12:40 - 14:30 |
Lunch Break Time |
TUESDAY 9 OCTOBER afternoon |
|
14:30 - 17:30 |
CIVIL ENGINEERING (part 2) |
14:30 - 17:30 |
AUTOMOTIVE (part 3) |
14:30 - 17:30 |
ENERGY |
14:30 - 17:30 |
MANUFACTURING SYSTEMS & MACHINES |
14:30 - 17:30 |
SYSTEM LEVEL SIMULATION (part 2) |
14:30 - 17:30 |
TRANSPORTATION (part 2) |
14:30 - 17:00 |
Workshop | Workflow Modeling for Collaborative Engineering A great method to boost your Project Management efficiency |
14:30 - 17:00 |
Workshop | Digital Twin, la nuova dimensione della simulazione numerica: un workshop interattivo e con una visione alto manageriale delle logiche di business derivanti (part 2) |
14:00 - 18:00 |
BEST PRACTICES AREA |
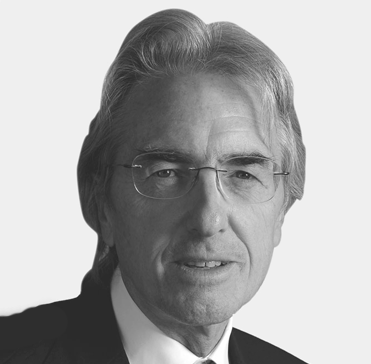
9:30
Stefano Odorizzi
EnginSoft, CEO and Co-founder
“Welcome”
Graduated in Civil Engineering in 1973, Stefano Odorizzi started his activity as researcher in 1976 at University of Padova, where he holds the course of Solid Mechanics. CEO and co-founder of EnginSoft, multinational consultancy company engaged in Simulation Based Engineering Science, he actively promotes numerical simulation for research activity, with particular attention for manufacturing process, metallurgy, multi-disciplinary and multi-objective optimization. Since 1977, he has been Project leader of a large number of EU co-funded research projects (like COMETT, CRAFT, BRITE-EURAM, MURST, EU-RTD); he is an active member of several associations (ISOPE, ASM Europe, AICAP, AIM, ATA, NAFEMS) and he plays an important role within prestigious European Networks (MACSinet, FENET, INGENET, TECHNET). His commitment in numerical simulation dissemination is witnessed by his many initiatives as General Manager of EnginSoft, in academic research and advanced training and education.
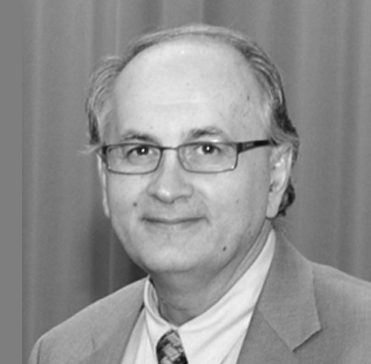
9:45
Mario J. Felice
Ford Motor Company, Global Manager of Powertrain NVH & Systems CAE Dept.
“Providing the Transformational Means to a New Era of Sustainability and Mobility Automotive Application to the Simulation of Powertrain NVH (Noise, Vibration & Harshness)”
The automotive engineering community is now confronting the largest technological transformation since its inception. Recent advancements related to the electrification of powertrains for more efficient consumption and cleaner emissions, the reinvention of the battery with fast wireless charging capabilities to fully replace the current fuel driven vehicles and finally the advent of fully autonomous vehicles.
The car as we know it today will totally change! It will have a so-called “soul” and will be an extension of your personality which you can talk to, can read your face and lips, and would know your mood and feelings as it transports you from point A to point B. The whole concept of passenger transportation is being transformed into a Safer, Healthier and Smarter Environment.
The challenges ahead for automotive engineers are enormous and SIMULATION will be playing a very important role in delivering these Smart Vehicles in a very demanding Smart World.
Mr. Felice is Global Manager of Powertrain NVH CAE engineering at Ford Motor Company. He heads a large team of well over 100 CAE engineers located in North America, Europe, Australia and India.
He’s responsible for all the analytical support of Ford’s global powertrain development programs with the goal of delivering best NVH refinement with respect to Smoothness, Quietness and Sound Quality.
Mr. Felice has been employed with Ford Motor Company for over 40 years. During this time he's held a number of positions specializing in design and analysis of engine components and sub-systems, as well as full powertrain system.
He has published and presented at many international symposiums and conferences and earlier this year he’s been elected member of the NAFEMS Council (Board of Directors). NAFEMS is the International Society for Simulation Engineering.
Mr. Felice holds degrees in Bachelor of Science in Mechanical Engineering from the Fairleigh Dickinson University (New Jersey) and Masters of Science in Mechanical Engineering from the University of Michigan.
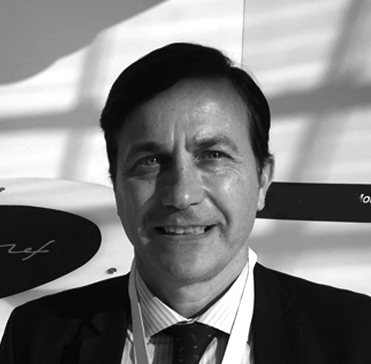
10:05
Gennaro Monacelli
CNH Industrial, Head of Design Analysis and Simulation and Material Engineering
“The future of Simulation in Agricultural Machinery towards 2050!”
CNH Industrial (CNHi) is a global leader in the capital goods sector that designs, produces and sells agricultural and construction equipment, trucks, commercial vehicles, buses and specialty vehicles, in addition to a broad portfolio of powertrain applications. Specifically, in the agriculture business CNHi represents one of the major full-line manufacturer which produces, with different brands, all the following products: Tractors, Planting & Seeding, Application equipment, Harvesting machines, Tillage tools, Windrowers, Mowers and Conditioners, Forage Harvesters and Blowers, Balers, Loaders and Attachments, Utility vehicle, Advanced Farming Systems and other products.
In the last decades, the agricultural machinery market has become highly competitive and the manufacturers of agricultural equipment have been pushed to continuously innovate their products, increasing the performances, the quality and reliability of their machines. We have seen that ‘digital simulation’ can accelerate the process of the Agricultural Machinery Design and improve the machine performances. For this reason, at CNHi we have introduced the digital approach in all the phases of the new product development process, with the goal to simulate digitally the whole Product and its performances. Our design team, starting from the early stage of the new product design, develops the complete digital representation of the Product (Digital Mock-Up) and the Plant (Virtual Manufacturing). Another big step is to identify the vehicle mission in order to reproduce on the test bench the different manoeuvres that the test engineers perform in the field (from the field to the bench). Finally, the simulation team reproduces on computer all the vehicle missions on the computer (going from ‘the bench to the math’). At this point we need to able simulate in accurate way all the range of operations and conditions that machines must perform in field. For this reason, a big area of our simulation team is dedicated to simulating the different seeds, soils and crops (in various stages of being processed), that can change their properties depending on the location and seasonal conditions. In fact, the variability of these properties can have a strong influence on the machine performances.
Having the ‘complete digital model’ of the new product, the Virtual Reality Centre has become the place where all the stakeholders of the product platform team executes the design reviews, analyses alternative solutions and deliberates product and process solutions. Using the immersive virtual environment (VR simulators), we can include in the design loop also members of the Brand & Marketing, Customers & Dealers that can evaluate the product features some years before the market launch of the new product.
The expected benefits of using Virtual Simulation are, therefore, the reduction of development time (it enables the concurrent engineering), the reduction of development costs (better design through virtual pre-checks, less modifications and less physical tests) and the quality increase (a product that fits perfectly with customer requirements).
Gennaro is the Simulation and Material Engineering world-wide responsible for CNH Industrial.
From 2014 to 2016 he was the Responsible of Innovation Department for all CNH Industrial Sectors and at the same time President of ALTRA SPA, Center of Excellence for the study of ALternative TRActions.
From 2008 to 2014 he covered the role of simulation director for agricultural and construction machinery at Fiat Industrial.
From 2006 to 2008 he worked at the Centro Ricerche Fiat as head of the "Intersectorial Methodology Innovation Master Plan". From March 1990 to June 2006 he worked in the area of Research & Development of the FCA (Fiat Chrysler Automobile) with increasing responsibility roles.
In 2000 he was CEO of the PRODE Consortium (Product Design) composed of ELASIS (FCA) and the University of Naples Federico II, and President of the SCIRE Consortium, composed of ELASIS and the University of Rome Tor Vergata. During the same period he held the position of Adjunct Professor of "Automobile Construction and Industrial Standardization" at the "Second University of Naples" and the "University of Naples Federico II" for about 10 years. He graduated in electronic engineering at the University of Naples Federico II.
From 2016 he is a member of the Board of Directors of the CRIT research consortium on behalf of CNH Industrial and President of the regional section of the GDF association (FIAT Director Group).
From 2017 he is in the Mentor Board of the ASTER, which is the Consortium for innovation and technology transfer of Emilia-Romagna region.
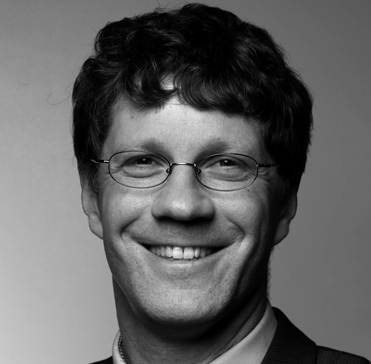
10:25
Stefan-Alexander Schneider
University of Applied Sciences Kempten, Professor of Advanced Driver Systems and Coordinator of the Master´s Course
“From ADAS to AD: Enabling the Disruption”
The presentation gives an overview about the challenges of the disruption from ADAS to AD and the key role of the modeling and simulation tools.
Prof. Dr. Schneider is sponsored Professor of Advanced Driver Systems and coordinator of the newly founded Master´s Course at the University of Applied Sciences Kempten.
Prof. Dr. Schneider studied Mathematic and Physic at the Technische Universität München, Germany, concluding with a diploma in 1995 and a Doctor rer.-nat., Mathematics and Computer Science in 2000. His first industry position was with Infineon Technologies AG where he worked as a development engineer in the department of Advanced Technology Software.
From 2001 – 2003, Prof. Dr. Schneider was with Axxom Software AG where he designed and developed mathematical optimization methods as a Senior System Analyst. Furthermore, he worked as Methods Engineer at BMW AG where he was concerned with Process, Method and Tool for Functional and Software Development, for Modeling Multi-domain Physical Systems, in particular with the programming language Modelica.
10:45 - 11:15 Coffee Break Time
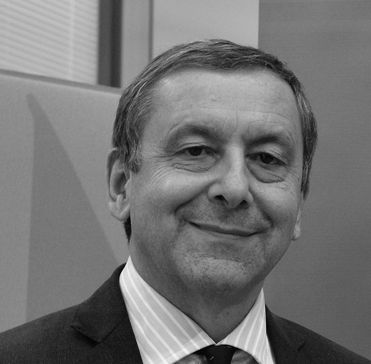
11.15
Francesco Profumo
Fondazione Bruno Kessler, President
"Future built on Artificial intelligence From Deep Competencies built in 30 years of Research to an Innovative Vision for the AI of the Future"
FBK built the future on a new generation of Artificial Intelligence, which does not replace humans at work, in their life but collaborate with them.
FBK*AI for citizens, which makes the city more livable, enjoyable, and safe.
FBK*AI for humans who enjoy an healthy style of life.
FBK*AI that lets machines and people work together, in a more productive, safe, pleasant, enjoyable factory.
FBK*AI for humans who respect the environment and its resources.
FBK*AI that helps humans to discover the secrets of world and matter physics.
Francesco Profumo (M’88-SM’90) was born in Savona, Italy, in 1953. He is Professor of Electrical Machines and Drives at Politecnico di Torino and Adjunct Professor at University of Bologna. He was Visiting Professor at University of Wisconsin – Madison (1986-1989), at Nagasaki University (1996-1997), at Czech Technical University (1999) and University of Cordoba (2004 and 2005). Dr. Profumo was the Dean of the Engineering Faculty at the Politecnico di Torino (2003 to 2005) and the Rector of the Politecnico di Torino (2005 to 2011).
He has been appointed as President of CNR (National Research Council) in July 2011 and as Italian Minister of Education, University and Research (MIUR) in November 2011. Prof. Profumo is the Chairman of Bruno Kessler Foundation, the Chairman of Fondazione Compagni di Sanpaolo, the Chairman of Turin Campus ESCP, the Chairman of SAFM.
His fields of interest are power electronics conversion, high power devices, applications of new power devices, integrated electronic/electromechanical design, high response speed servo drives, new electrical machines structures, power conditiong systems for fuel cells applications.
He published more than 250 papers in International Conferences and Technical Journals. Dr. Profumo won the IEEE-IAS second prize paper in 1991(USA) and in 1997 (USA), the IEEE-IAS first prize paper in 1992 (USA) and the JIEE-IPEC first prize paper in 2005 (JAPAN).
He was awarded by the Signum Aureum Facultatis Mechanicae Universitatis Miskolciensis, July 1, 2000, University of Miskolc (Hungary), by the Honorary Professorship, University of Cordoba (Argentina),
August 11, 2004, by the Honorary Doctor Degree, Technical University of Riga (Latvia), October 12, 2006, by the Honorary Doctor Degree, Politechnica of Bucarest (Romania), June 15, 2007, by the Honorary Doctor Degree, University of Miskolc (Hungary), June 26, 2007, by the Honorary Professorship, Jiao Tong University, Xi An (China), September 11, 2007, by the Honorary Professorship, Henan Polytechnic University, Jiaozuo (China), September 27, 2009, by the Honorary Doctor Degree, Politechnica of Tirana (Albania), October 1, 2009, by Honorary Professorship, Tongji University, Shanghai (Cina), June 20, 2012 and by Honorary Professorship, Luoyang Normal University, Luoyang (Cina), November 22, 2013.
Further awards: China Awards by Italy_China Foundation (2009), Certificate of Appreciation by Fulbright Commission (2009), Orden Universidad Javeriana by Javeriana University (Bogotà, Colombia) (2010), Escudo de Oro by University of Antioquia (Medellin, Colombia) (2010),Lion d'Oro by Lion International (Torino) (2008), Award Valdo Fusi (Torino) (2011), Award Guido Carli (Rome) (2011) and Award Pericle (Torre di Ruggiero) (2013).
He has been the Chairman of the G8 University Summit 2009, (Torino) (2009) and the Chairman of the Columbus Association (55 European and Latin American Universities) (2006-2011).
He has been the Chairman of IREN Group (2013-2016), Member of the Board of Unicredit Private Bank (2008/2010), of the Board of Il Sole 24 Ore (2007/2009), of the Board of Fidia (2007/2011), of the Board of Telecom (2011), of the Board of Pirelli (2011) and of the General Committee of Unicredit Private Banking (2011).
He is Member of Academia Europaea - Physics and Engineering Section (2010) and member of the Accademia delle Scienze (2008).
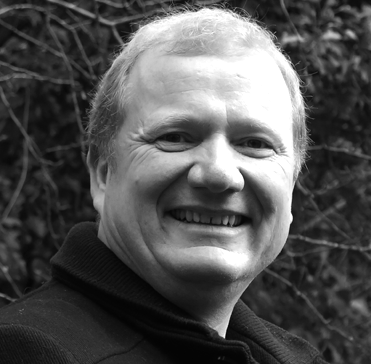
11.35
John Goodacre
University of Manchester, School of Computer Science, Professor of Computer Architectures
“Will your software need to change for exascale? The challenges on power efficient hardware”
Prof. John Goodacre holds a Professorship in Computer Architectures in the School of Computer Science at the University of Manchester while also being the Director of Technology and Systems in the Research Group at ARM Ltd and is co-founder and Chief Scientific Officer at Kaleao Limited. His career has included the realisation of the first scalable commodity telephony platform, the introduction of the first real-time collaboration tools shipped in Microsoft Exchange 2000, while more recently, was responsible for the design and introduction of the ARM MPCore multicore processor and associated technologies. His roles today extend across both academic and industrial research topic, focused around web-scale servers, exascale efficient systems and ubiquitous computing, while also driving forwards the technological vision for the Kaleao systems roadmap. This gives him a unique hardware and software background with experience from embedded to the largest of big data and HPC systems. He sits on various advisory boards at both national and European level and is a frequent conference speaker.
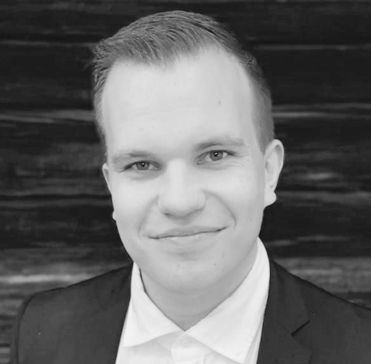
11.55
Juho Raukola
Wärtsilä Corporation, Additive Manufacturing innovation expert
“Big thinking more than top technology – A smart approach for Additive Manufacturing”
Global megatrends such as artificial intelligence, advanced data analytics, simulation, and the Internet of Things will inevitably have a massive impact on the manufacturing industry. This will be realized through rapid shifting from an experience and physical product-based industry to businesses based on a virtual, data-driven model of the product and the whole production ecosystem. In terms of the ever-increasing need for tailoring and case-specific optimization of products to improve overall performance, using a virtual environment for as long as possible can be extremely beneficial. However, converting these fine-tuned digital models into real, physical products can be problematic due to the increased amount of customization and complexity, which is further translated into increased costs and lead times.
Additive Manufacturing (AM, also 3D printing), thanks to the design freedom it provides, can be effectively utilized to fulfil the requirements of modern industry. Custom-made tooling can be produced on-demand for a fraction of the costs of conventionally manufactured tools, and the potential for high-performance end-use parts is endless – both in metal and polymer materials. Being an inherently different manufacturing process to conventional subtractive methods, however, a significant investment in knowledge must be made in order to unlock all the potential that Additive Manufacturing makes available. This speech will shed some light on Wärtsilä’s insights into the current and near-future potential of Additive Manufacturing, and how to implement it in a smart way, illustrated with concrete business case examples from the real-life factory-floor level.
Wärtsilä is a global leader in smart technologies and complete lifecycle solutions for the marine and energy markets. By emphasising sustainable innovation, total efficiency and data analytics, Wärtsilä maximises the environmental and economic performance of the vessels and power plants of its customers.
Juho Raukola is an Innovation Expert in Wärtsilä Corporation, and is the main specialist in the area of Additive Manufacturing within the company. He is responsible of forming and implementing utilization strategy for AM technologies in company, and building up global AM ecosystem for supporting current businesses and creating completely new value chains in Marine & Energy sectors enabled by AM. Raukola did his Master’s thesis “Characteristics and applications of metal additive manufacturing in 4-stroke engine manufacturing process” in Wärtsilä’s Vaasa site in Finland during 2017, and in January 2018 was then appointed as the first Additive Manufacturing Engineer in the history of this 18 000-people company. In June, he was promoted into his current position in Wärtsilä’s Global Smart Manufacturing organization, working on recognizing and developing feasible applications for additive manufacturing both in end-use components and the manufacturing processes of the company’s products, and fostering new kind thinking the smart approach for Additive Manufacturing requires.
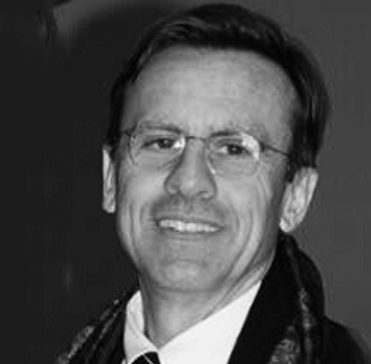
12.15
Aleksandar Jovanovic
European Virtual Institute for Integrated Risk Management (EU-VRi), CEO
“Common methodology and common database for the indicator-based assessment of resilience of critical infrastructures”
Resilience of modern societies is largely determined by and dependent on resilience of their critical infrastructures such as energy grids, transportation systems, governmental bodies and water supply. This is clearly recognized by the European Union in its policies and research agenda, such as the DRS (Disaster-Resilience) actions and projects safeguarding and securing society, including adapting to climate change. In this context, the issue of “measuring resilience” has an important place and it is tackled primarily by means of indicators, within the DRS-14 line of calls. The overall goal of the current research agenda is to improve current approaches by providing an innovative “holistic” methodology for assessing resilience of critical infrastructure. The EU research project SmartResilience propose a common methodology across all critical infrastructures and all types of hazards or threats based on resilience indicators. Generally, indicators come from a variety of sources including existing standards, public documents, company practices, literature, and similar, but are also largely defined within the project. The resilience indicators are stored in a common database. The results of the resilience assessment can be used in various ways. One is to compare with previous assessment, i.e. providing a trend showing how the level of resilience is progressing. Since the calculation is performed on all levels of the model (indicator, issue, phase, threat, critical infrastructures and area/city level), it is also possible to "drill down" and identify the reason for an increase or decrease in resilience compared to the previous assessment. Another use is to compare with other cities, areas or critical infrastructures, i.e. to benchmark against others, which provides the opportunity to learn from others. The resilience of a city/area or a critical infrastructure can also be assessed by imposing a set of threats (including defined challenges such as interactions and cascading effects), i.e. stress testing the resilience ability of the city/area/critical infrastructure, and compare the results with predefined criteria. The concept presented is practically applied with the support of new tools: the large database of indicators, tools for the assessment of the resilience level, tools for resilience monitoring, big data analysis tools and the advanced visualization tools.
Aleksandar JOVANOVIC, (1953): Worked in industry (energy), for the European Community (Belgium, Italy), in research (Argonne Ntl. Lab, Steinbeis, EU-VRi) and at universities (Germany, Japan, Serbia, France, China). Since 2001, he is the director of the Steinbeis Advanced Risk Technologies Group in Stuttgart, Germany providing consultancy in the areas of risk assessment and risk management for industry and public sector. As from 2006 he is also the CEO of the European Virtual Institute for Integrated Risk Management (EU-VRi) and the EU Project Director and lecturer at ZIRIUS (Research Center for Interdisciplinary Risk and Innovation Studies, University of Stuttgart). He is a full professor at Steinbeis University Berlin and University of Novi Sad. His other current and previous assignments include Italy (Politecnico di Milano), France (Ecole Polytechnique), Japan (University of Tokyo), USA (La Jolla), China (Beijing Capital University) and other countries.
A. Jovanovic has a long-year professional experience as project manager of many large international/multinational projects in the area innovation management, new technologies, advanced data analysis and data mining, and related areas. Main clients in the projects have been from the EU, national governments (Norway, Belgium, Japan…), industry, utilities, insurances companies, R&D and academia. Main topics covered by the current projects deal with risk management in industry (e.g. for insurance, power, process) and include HSSE (Health, Safety, Security, Environment), RCM (Reliability Centered Maintenance), RBI (Risk-Based Inspection), KPIs (Key Performance Indicators) and RCFA (Root Cause Failure analysis) and Resilience. Sample projects managed by him include iNTeg-Risk (www.integrisk.eu-vri.eu, 19.3 million €, 80+ partners), EskomRBI (RBI for power plants in South Africa, 40,000 MWe) or SmartResilience (Resilience Indicators for critical infrastructures in Europe, www.smartresilience.eu-vri.eu).
As a “risk practitioner” A. Jovanovic has contributed to the global risk community by a number of actions, such as Convener and main author of the European standards CEN-CWA 15740 (“RBI”), EN16991:2018 (“RBIF – Risk-Based Inspection Framework”) and CEN-CWA 16449:2013 (“Management on New Technologies-Related Risks”), now being developed as ISO 31050 (“Guidance for managing emerging risks for enhanced resilience”). He is a coauthor of the milestone studies/books like the “Future Global Shocks” issued by OECD (2013) of “Expert Systems in Structural Safety Assessment” (Springer, 1987), as well other 7 books and over 200 publications. He speaks fluently French, Italian, English, German and Serbian, and reads Spanish and Russian.
Unfortunately Professor Jovanovic will not be able to attend the conference, so his speech will be delivered by Mr. Svetoraz Eremić.
Svetozar Eremić is the HSE (Health, Safety, Environment) manager/director in Pančevo Oil Refinery. He has a wide experience on production processes, maintenance activities and reliability strategies and development in refinery units that he gained while working on various positions in Pančevo Oil Refinery. He is Risk Based Inspection (RBI) and Reliability Centred Maintenance (RCM) Certified Expert, Steinbeis University, Berlin. He was NIS leader in the FP7 project iNTeg-Risk - Early recognition, Monitoring and Integrated Management of Emerging, New Technology Related Risks , NIS leader in the EU project SmartResilience and the Chair of the End-User Advisory Group.
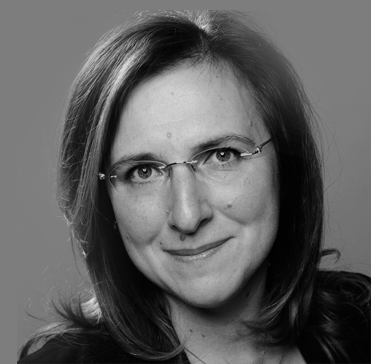
12.35
Natalia Konchakova
Magnesium Innovation Centre MagIC of the Helmholtz Zentrum Geesthacht, Senior Scientist
“Materials Modeling Translation: How Industrial Challenges can be addressed by Modeling and Engineering Simulations?”
Involving of Materials Modelling as well as Engineering Simulation into business decision to develop and manufacture new products, perform novel multi-functional materials and systems, study and analyze the life-cycle performance and properties of engineering structures are considered as a European Science & Technology strength. Industry needs to use modelling tools and approaches for digital analyse of materials, products and manufacturing process, which allow varying some parameters to find the optimal product properties, design and characteristics. Integration of materials modelling to solve the industrial problem is the focus of European Materials Modelling Council (EMMC). The modelling and digital analysis offers unique insight into properties and in-service behaviour of materials, manufacturing process and understanding of the physics of materials, devices and processes. On the other side, modelling reduce product development time as well as costs and hardware for testing [1].
Materials modelling as well as digital twins are important parts of the modern business decision making. However, they need far more implementation and use in manufacturing industry to reap their full economic impact. Unfortunately, it is the big issue to find the bridging between the industrial challenges and scientific/ academic innovations, needed for the realisation of the industrial tasks.
How industry, especially SMEs, can find the modelling specialists or suitable modelling workflow to solve the concrete applied problem? Who can give the information regarding the costs of the modelling implementation and economic benefits from the modelling projects? The translation of industrial case into modelling solution is performed by Translators. They are primary players at the interface between industrial end-users on the one hand and software owners and modellers on the other hand. Translators support the usage of materials modelling in industrial R&D to the same level as experiments are used today.
The challenges and possibilities for wider industrial adoption of modelling and engineering simulations are discussed in the talk. The EMMC Materials Modelling Translation concept is presented and explained in details.
Dr. Natalia Konchakova is a Senior Scientist at the Magnesium Innovation Centre MagIC of the Helmholtz Zentrum Geesthacht - Centre for Materials and Costal Research, and Vice-Leader of the Working Group Translators of the European Materials Modelling Council (EMMC). She works in the field of Materials Modelling and Simulation of Lightweight Metal/ Fibre-Reinforced Polymer Composites Structures, Computation analysis of material damage and surface degradation due to corrosion and intensive mechanical loading as well as numerical prediction of crack propagation in engineering structures. Development of the European Materials Modelling Translation concept is the focus of the current activity of Dr. Konchakova.
13:00 Lunch Break Time
Collateral Events
Lunedì 8 Ottobre 2018, ore 14:00 | Seminario
Co-design di componenti colati e forgiati | Come il dialogo con i fornitori può migliorare la qualità e le performance dei vostri prodotti
Il seminario (della durata di 3 ore) ha lo scopo di illustrare le dinamiche dei processi produttivi fusori e di deformazione plastica dei metalli, nonché alcune tecniche di progettazione e ottimizzazione integrate mirate alla realizzazione del componente secondo le specifiche di capitolato.
The three-hour workshop (in the Italian language) will illustrate the dynamics of the foundry and metal forming production processes, as well as some integrated design and optimization techniques targeted at the realization of a component according to its technical specifications.
8 - 9 OCTOBER 2018 | workshop
Exascale Computing Workshop: Experiences and Best Practices for Porting Applications to Emerging HPC Architectures and Platforms
This workshop aims to provide a forum for vanguard users and developers in the HPC arena to share their experiences and achievements around the various European platforms developed by the ExaNeSt, ExaNoDe, Ecoscale and EuroExa projects.
Whether you are designers of new hardware architectures or system components; software or application developers; or users that need to exploit these massive processing capacities, everyone has something valuable to contribute to the discussion in the development of this next frontier of HPC.
9 OCtOBER 2018, HOURS 9:30 - 12:30 | WORKSHOP
Geometric Dimensioning and Tolerancing (GD&T) Workshop
This workshop will demonstrate how companies can leverage state-of-the-art GD&T methods and instruments to create more robust hi-tech products while containing production costs.
It will present the best methods and instruments available to identify the ideal compromise between the Designer’s demands to meet the end-product requirements, and Manufacturing’s need to rapidly and cost-effectively produce and assemble the components.
9 OTTOBRE 2018, ore 9:00 - 13:00 | Tavola Rotonda
Industria 4.0: Valorizzare gli investimenti con competenze e tecnologie software di Industrial Analytics. Come utilizzare i dati per accrescere la competitività delle imprese 4.0
Le indicazioni che ci si propone di fornire ai partecipanti alla Tavola Rotonda vogliono essere un tentativo di dare delle risposte alle classiche domande che si pongono imprenditori e manager: Di cosa si sta parlando? Perché dovrei farne uso? Chi e come impiega già queste soluzioni? Come potrei applicarle? Quanto mi costerà farlo e quanto sarà il rendimento di questo investimento? Quali competenze strategiche sono irrinunciabili in questa fase?
This panel discussion will take place in the Italian language.
9 OCTOBER 2018, HOURS 14.30 – 17.00 | workshop
Workflow Modeling for Collaborative Engineering
A great method to boost your Project Management efficiency
Workflow Modeling has become a fundamental best-practice to quickly develop the high-quality, complex products necessary to compete in today’s rapidly changing markets.
You’ll discover how to build an integrated workflow, managing and automating all the logical steps of the engineering process, while exploring how efficient workflow-modeling simplifies and accelerates the entire design process.
9 OTTOBRE 2018, ORE 10:00 - 17:00 | WORKSHOP
Digital Twin, la nuova dimensione della simulazione numerica: un workshop interattivo e con una visione alto manageriale delle logiche di business derivanti
Durante la mattinata, EnginSoft e PTC presenteranno lo stato dell’arte delle metodologie di implementazione e delle tecnologie in ambito Digital Twin, mentre nel pomeriggio si costituiranno dei tavoli di lavoro a tema, che coinvolgeranno sia gli iscritti al workshop sia i tecnici di EnginSoft e PTC, per valutare ed evolvere i casi applicativi che verranno trattati.
This workshop will take place in the Italian language.
9 OCTOBER 2018, HOURS 9:00 - 13:00 | workshop
RECAM – Rapid Reconfiguration of Flexible Production Systems | Final Exploitation Event
The main goal of RECAM is to develop and demonstrate the next generation of flexible production systems leaning on the reconfigurable modular production resources, associated engineering tools and control systems.
The exploitation event has the aim to showcase the RECAM approach and results to interested Stakeholders from industry and academia.
Technical SESSIONS
Click on the rows to read the details
Monday 8 October 14:00 - 18:00
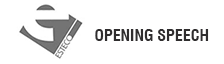
SPEAKER |
COMPANY |
TITLE OF PAPER |
|||
---|---|---|---|---|---|
14:00 |
Emiliano Costa |
RINA Consulting |
Shaped charge: a comparative study of jet penetration into a multi-layered target |
||
|
|||||
14:20 |
Daniele Santoro |
Elettronica SPA |
Roadmap towards a collaborative multi-physics simulation workflow for defense applications |
||
|
|||||
14:40 |
Alberto Clarich |
ESTECO SpA |
Combining Adjoint Optimization and mesh morphing for CFD applications |
||
|
|||||
15:00 |
Andrew Chinn |
International TechneGroup Limited |
Robust Morphing of CAD Geometry based on Simulation Results |
||
|
|||||
15:20 |
Andreas Vlahinos |
Advanced Engineering Solutions |
Practical Techniques for Design Optimization of Lattice Structures |
||
|
|||||
15:40 |
Coffee Break Time |
||||
16:10 |
Giuseppe Totaro |
Leonardo SpA |
Development of a software application for comparative manufacturing costs analyses |
||
|
|||||
16:30 |
Emiliano Costa |
RINA Consulting SpA |
FSI optimization of industrial airplanes: the P180 Avanti EVO study |
||
|
|||||
16:50 |
Enrico Serra |
INFN- TIFPA |
Thermal Management of the ALPIDE Space Module for Particle Tracking |
||
|
|||||
17:10 |
Viktor Pocajt |
Key to Metals AG |
Material selection for lightweight design in aerospace and defence engineering workflow |
||
|
Monday 8 October 14:00 - 17:30
SPEAKER |
COMPANY |
TITLE OF PAPER |
|||
---|---|---|---|---|---|
14:00 |
Henning Dombrowski |
GKN Driveline |
Gearbox lubrication studies with meshless CFD methods |
||
|
|||||
14:20 |
Luca Martinelli |
Drive System Design Ltd |
Increasing power density of EV E-Motors via optimised cooling simulation methods |
||
|
|||||
14:40 |
Sami Ojala |
Wärtsilä Finland Oy |
Designing and analysing the cooling of a medium speed engine piston using MPS method |
||
|
|||||
15:00 |
Elisabetta Fava |
Comer Industries SpA |
Oil path prediction and optimization for high speed transmissions with ParticleWorks |
||
|
|||||
15:20 |
Roberta Messina |
HPE COXA |
HPE COXA: Particleworks application in Automotive Industry |
||
|
|||||
15:40 |
Coffee Break Time |
||||
16:10 |
Sunao Tokura |
Prometech Software, Inc. |
Recent Progress of Particle Method MPS in Industrial Application |
||
|
|||||
16:30 |
Iago Fernandez |
Gompute |
Efficient CAE workflows in hybrid HPC systems for the Automotive Industry |
||
|
|||||
16:50 |
Stefano Pizzuto |
FCA |
Multi disciplinary optimization of engine suspension stiffness |
||
|
|||||
17:10 |
Klaus Hofwimmer |
Magna Powertrain |
Fatigue Analysis using FEMFAT inside ANSYS Workbench |
||
|
|||||
17.30 |
Wolfgang Gentzsch |
The UberCloud |
The Timing is Right for CAE in the Cloud |
||
|
|||||
Tuesday 9 October 9:30 - 17:00![]() |
|||||
9:30 |
Giancarlo Gotta |
FCA |
Moving automotive thermal tests from real world roads to laboratory facilities, 1d simulation supporting |
||
|
|||||
9:50 |
Ignacio Hernández |
Ricardo Prague |
Flame-wall interaction modelling for pre-chamber combustion in lean burn gas engines |
||
|
|||||
10:10 |
Michael Klein |
INTES |
Influence of Contact Linearization on Brake NvH Behavior |
||
|
|||||
10:30 |
Francesco Fortunato |
FCA Italy |
A model for automotive tank evaporative emission prediction |
||
|
|||||
10:50 |
Coffee Break Time |
||||
11:20 |
Giuseppe Cicalese |
R&D CFD SRL |
Free-form and parametric optimization of powertrain components using CFD: from the intake to the exhaust line |
||
|
|||||
11:40 |
Fabrizio Mattiello |
Fiat Research Center |
Dual function air outlet numerical optimization |
||
|
|||||
12:00 |
Petr Cerveny |
Ricardo Prague Technical Center |
Application of WAVE-RT and rCube2 on running engine to reduce emissions and eliminate physical sensors |
||
|
|||||
12:30 |
Lunch Break Time |
||||
14:30 |
Emiliano Di Tullio |
FCA Italy |
Direct Cooling PHEV Battery 1d Analysis |
||
|
|||||
14:50 |
Athanasios Papadopoulos |
BETA CAE Systems |
Simulation results communication through a VR Collaboration Environment: a car's headlamp analysis case |
||
|
|||||
15:10 |
Fatih Yasin Elagoz |
CMS Jant ve Mak. San. A.S. |
Preprocess Automation of ISO 7141 13° Impact Simulation for Light Alloy Casted Wheels |
||
|
|||||
15:30 |
Coffee Break Time |
||||
16:00 |
Antonio Ercoli |
Cubit s.c.a.r.l. |
Comparison of two multiphase procedures on a commercial vehicle in rain conditions |
||
|
|||||
16:20 |
Siva Srinivas Babu Beesetti |
MERCEDES BENZ RESEARCH & DEVELOPEMENT INDIA |
Accelerated Digital Approach for Development of Grommet |
||
|
Monday 8 October 14:00 - 17:30
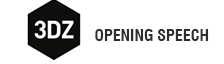
SPEAKER |
COMPANY |
TITLE OF PAPER |
|||
---|---|---|---|---|---|
14:00 |
Lorenzo Scano |
Studio Scano Associato |
Impact of Weld Residual Stresses on the Creep Life of High-Temperature Pressure Components |
||
|
|||||
14:20 |
Mariagrazia Vottari |
Key to Metals |
Optimization of material properties workflow and selection in CAE |
||
|
|||||
14:40 |
OZAN MERT BALCI |
BOSCH TERMOTEKNİK |
A waste heat recovery system by storing energy on phase change material in combi boilers |
||
|
|||||
15:00 |
Michael Gasik |
Aalto University Foundation |
Microstructure-fluid interaction in 3D--printed silicone for laryngeal medical implants |
||
|
|||||
15:20 |
Koji Yamamoto |
CYBERNET SYSTEMS CO.,LTD. |
Multiscale and optimization analysis of lattice structure produced via additive manufacturing |
||
|
|||||
15:40 |
Coffee Break Time |
||||
16:10 |
Fara Cioeta |
INFN |
Simulation of thermo-mechanical effects produced by a highly focused radiation applied on a material: developing of a multi-purpose APDL script for the physical characterization |
||
|
|||||
16:30 |
Stuart Baker |
Granta Design |
Materials and simulation: from CAE to ICME, a 2040 vision |
||
|
|||||
16:50 |
Taku Ozawa |
JSOL Corporation |
Integrated simulation system for soft materials, J-OCTA |
||
|
Monday 8 October 14:00 - 17:30
SPEAKER |
COMPANY |
TITLE OF PAPER |
|||
---|---|---|---|---|---|
14:00 |
Alexandre Mugnai |
ESTECO |
ADAS systems Robustness analysis and optimization: a way to assess the function’s performance |
||
|
|||||
14:20 |
Francisco Chinesta |
ESI Group |
Hybrid Twin: A new paradigm for the industry and society4.0 - Enriching technology and humans |
||
|
|||||
14:40 |
Francesco Rizzi |
Center for Biomolecular Nanotechnologies, Istituto Italiano di Tecnologia |
Recovery of Mechanical Energy from fluids for the feeding of an IoT node for monitoring of diesel engine exhaust gases |
||
|
|||||
15:00 |
Alessandro Cinciripini |
EnginSoft SPA |
Development of a FSI Methodology to Simulate a Piezoelectric Energy Harvester System from Engine Exhaust Gases |
||
|
|||||
15:20 |
Andrea Francesco Sola |
COMAU |
Passive upper limb support exoskeleton: from the technical specifications to the market |
||
|
|||||
15:40 |
Coffee Break Time |
||||
16:10 |
Corrado Groth |
University of Rome "Tor Vergata" |
The medical digital twin assisted by Reduced Order Models and Mesh Morphing |
||
|
|||||
16:30 |
Lorenzo Pranovi |
Istituto Nazionale di Fisica Nucleare * Laboratori Nazionali di Legnaro |
Virtual Reality Application in a Nuclear Accelerator Facility |
||
|
|||||
16:50 |
Maiki Vlahinos |
Advanced Engineering Solutions |
Conceptual Design tools for Innovation Engineering |
||
|
|||||
17:10 |
Guido Colombo |
Orchestra Srl |
IoT stack to bridge the gap between the Operation technologies and the ICT of the SME’s |
||
|
|||||
17:30 |
Emanuele Zanin |
CST – Computer Simulation Technology GmbH |
Smart Watch Antenna Design |
||
|
Monday 8 October 14:00 - 17:15
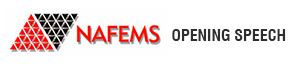
SPEAKER |
COMPANY |
TITLE OF PAPER |
|||
---|---|---|---|---|---|
14:00 |
Paul Goossens |
Maplesoft |
Functional Verification of Complex Engineering Designs using System-Level Modeling |
||
|
|||||
14:20 |
Erik Mazzoleni |
EnginSoft SPA |
1D and 3D coupling: the simulation approach and industrial applications |
||
|
|||||
14:40 |
David Holt |
Canada National Research Council |
Lowering the Risk of Transit Electrification with Informed, Model-Based Strategies |
||
|
|||||
15:00 |
Demetrio Scarfone |
Ansaldo Energia |
A Flywheel cooling design review by means of Flownex |
||
|
|||||
15:20 |
Kurt Zehetleitner |
B&R Industrial Automation |
Machine-level Virtual Commissioning for On-Time, On-Budget Innovation |
||
|
|||||
15:40 |
Coffee Break Time |
||||
16:10 |
Elio De Marinis |
EnginSoft SpA |
ANSYS Twin Builder: the new era of pervasive simulation |
||
|
|||||
16:30 |
Daniele Severi |
AVL Italy |
Numerical Challenges in Co-Simulation |
||
|
|||||
16:50 |
Takashi Iwagaya |
Cybernet Systems |
Moving boundary problem in System-level thermal analysis |
||
|
|||||
Tuesday 9 October 14:30 - 17:00 |
|||||
14:30 |
Manolo Venturin |
EnginSoft SpA |
State of the art of multi-domain system modeling |
||
|
|||||
14:50 |
Yann Debray |
ESI Group |
Scilab & SimulationX for preliminary design of electric motor |
||
|
|||||
15:10 |
Matteo Longoni |
Moxoff SpA |
Advanced modelling for industrial process design |
||
|
|||||
15:30 |
Coffee Break Time |
||||
16:00 |
Mugur Tatar |
QTronic GmbH |
Virtual ECUs and virtual validation of automotive control functions |
||
|
|||||
16:20 |
Armin Koelker |
Altia |
The UI: The Other Face of Your Digital Twin |
||
|
Monday 8 October 14:00 - 17:00
SPEAKER |
COMPANY |
TITLE OF PAPER |
|||
---|---|---|---|---|---|
14:00 |
Giuseppe Marulo |
Pierburg Pump Technology Italy Spa |
Dynamics Simulation and Experimental Validation of a Variable Displacement Vane Oil Pump |
||
|
|||||
14:20 |
Paolo Verziagi |
EMAK SpA |
Multi-axial and Vibrational Fatigue in ANSYS Workbench: First Applications |
||
|
|||||
14:40 |
Francesco La Mura |
Todeschini Mario Srl |
Development of a Digital twin for an enhanced performance of an HIL simulator |
||
|
|||||
15:00 |
Ivan Azzalin |
Electrolux Italia SpA |
System Level Simulation as Key Factor in the Development of Washing Machines |
||
|
|||||
15:20 |
Jacopo Ghilardi |
Lovato Electric Spa |
Multibody simulation of a switch disconnector |
||
|
|||||
15:40 |
Coffee Break Time |
||||
16:10 |
Dong-Hyup Shin |
FunctionBay, Inc. |
System Analysis using Multi-body Simulation Technology |
||
|
|||||
16:30 |
Barry James |
Romax Technology Ltd. |
Developing the Digital Twin for Gearboxes – capturing all relevant physical and multi-physical phenomena |
||
|
|||||
16:50 |
Ian McLuckie |
Advanced Integrated Engineering Solutions Ltd |
Solutions for fluid lubricated slider bearings |
||
|
|||||
17:10 |
Jan Hesse |
CFX Berlin Software GmbH |
Strategies for Reliable 3D CFD Simulation of Positive Displacement Machines |
||
|
|||||
17:30 |
Valentin Keppler |
Biomotion Solutions |
Modeling and simulation of biomechanical human body models in MBS by means of an automatic model generator |
||
|
Monday 8 October 14:00 - 17:30
SPEAKER |
COMPANY |
TITLE OF PAPER |
||||
---|---|---|---|---|---|---|
14:00 |
Stefano Ricci |
Ducati Motor Holding SPA |
Ride comfort optimization of a Ducati motorbike |
|||
|
||||||
14:20 |
Angelo Surini |
Hitachi Rail Italy |
Crashworthiness design according to the European Standard EN15227: description of the numerical/experimental methodology applied to the new MLA platform project |
|||
|
||||||
14.40 |
Andrea Cremoncini |
ISE Ingegneria dei Sistemi Elettronici S.r.l. |
Evaluating Optical Density by smoke propagation simulation in a railway coach |
|||
|
||||||
15.00 |
Juan Pablo Leiva |
Vanderplaats Research & Development, Inc. |
Structural Optimization: Evolution, Concepts and Applications |
|||
|
||||||
15:20 |
Michael Klein |
INTES GmbH |
Efficient Freeform Optimization for Stress Reduction on Complex Assemblies |
|||
|
||||||
15:40 |
Coffee Break Time |
|||||
16:10 |
Stefan Harries |
FRIENDSHIP SYSTEMS AG |
Massive Parameter Reduction for faster Fluid-dynamic Optimization of Shapes |
|||
|
||||||
16:30 |
Daniele Bruno |
MICAD srl |
Fluid dynamics optimization of a shaft-less rim-driven thruster |
|||
|
||||||
16:50 |
Marco Brivio |
BCOOL ENGINEERING srl |
CAE Tools In Marine Industry: Optimization of On-Board Thermal Comfort |
|||
|
||||||
17:10 |
Simone Bartesaghi |
Fluid4Engineering Srls |
Ventilation Inception for Kite Foil Surface Piercing Struts |
|||
|
||||||
17:30 |
Raffaele Ponzini |
CINECA |
LincoSim Web App: preliminary usage statistics and validation results |
|||
|
||||||
Tuesday 9 October 14:30 - 17:00![]() |
||||||
14:30 |
Francesco Testa |
AVL |
Guidelines for Transmission Simulation Using Both Traditional FVM and new SPH Approaches |
|||
|
||||||
14:50 |
Carlo Augusto Pasquinucci |
TecnoHit |
Learning from Results: Data Based Project based on CFD Simulations |
|||
|
||||||
15:10 |
Riccardo Testi |
Piaggio & C. SpA |
Fretting fatigue implementation in Workbench |
|||
|
||||||
15:30 |
Coffee Break Time |
|||||
16:00 |
Remo De Donno |
Industrie Saleri Italo Spa |
Design of Centrifugal Pumps by CFD Simulations and Surrogate-Based Shape Optimization |
|||
|
||||||
16:20 |
Antonis Perifanis |
BETA CAE Systems |
Simulation results compression for efficient Results Data Management |
|||
|
Tuesday 9 October 9:30 - 17:00
SPEAKER |
COMPANY |
TITLE OF PAPER |
|||
---|---|---|---|---|---|
9:30 |
Ennio Cortellini |
AMEU-ECA School |
Seismic safety Analysis of a base-isolated LNG tank |
||
|
|||||
9:50 |
Matteo Bruggi |
Politecnico di Milano |
Assessment of no-tension masonry-like structures using the Straus7 API |
||
|
|||||
10:10 |
Diego Neri |
Geodata SpA |
An optimized practical solution for construction of cross passage in soft ground mechanized tunnelling in urban area |
||
|
|||||
10:30 |
Giovanni Di Sciascio |
Studio Di Sciascio Srl |
Use of the pushover method for the seismic analysis of mixed frame-wall structures |
||
|
|||||
10:50 |
Coffee Break Time |
||||
11:20 |
Massimo Maffeis |
Maffeis Engineering SpA |
One Single Model: a new parametric approach to Megastructures |
||
|
|||||
11:40 |
Carmen Bernardini |
Politecnico di Milano |
Advanced automated procedure for the fatigue characterization of welded steel joints |
||
|
|||||
12:00 |
Ada Malagnino |
University of Salento |
Managing Critical Infrastructures with BIM: integrating the Analytical model |
||
|
|||||
12:20 |
Roman Martín Martín |
INGECIBER S.A. |
Construction process and cracking analysis of a tunnel, sequential analysis and actions of the influence of a building over the tunnel. Design of the steel, reinforced and prestressed structures with CivilFEM. |
||
|
|||||
12:40 |
Lunch Break Time |
||||
14:30 |
Francesco Del Viva |
SMStrutture |
Analysis and verification procedure for wooden panels structures by a general purpose FEM code |
||
|
|||||
14:50 |
Pawel Sosnowski |
SimScale GmbH |
Comparison of Finite Volume and Lattice-Boltzmann Methods’ performance in simulating building wind loads |
||
|
|||||
15:10 |
Simone Meduri |
Politecnico di Milano |
Explicit Lagrangian FEM for 3D Fluid-Structure Interaction Problems |
||
|
|||||
15:30 |
Coffee Break Time |
||||
16:00 |
Alessandra Aguinagalde |
Sapienza University of Rome |
Finding Shanley critical load under fire |
||
|
|||||
16:20 |
Mauro Madeddu |
FSC ENGINEERING SRL |
Fire behavior of self-supporting automated warehouses |
||
|
Tuesday 9 October 9:30 - 13:00
SPEAKER |
COMPANY |
TITLE OF PAPER |
|||
---|---|---|---|---|---|
9:30 |
Michele Zanni |
Fonderie Mario Mazzucconi |
Influence of process parameters on thermal fatigue and die life in a HPDC process for aluminum alloys |
||
|
|||||
9:50 |
Eleonora Battaglia |
New Olef |
Computer Aided Engineering (CAE) simulation for the design and production of an automotive structural component with tilting gravity die casting process |
||
|
|||||
10:10 |
Alessandro Zanirato |
Foseco |
Filling dynamics with tangential gates using virtual analysis |
||
|
|||||
10:30 |
Mario Priasco |
Teksid Aluminum |
Gating System Optimisation for the production of an aluminium engine head in gravity process |
||
|
|||||
10:50 |
Coffee Break Time |
||||
11:20 |
Elena Fiorese |
Fonderia Corrà SpA |
Predicting the final quality of cast iron parts through process simulation and optimization |
||
|
|||||
11:40 |
Nicola Gramegna |
EnginSoft SpA |
Digital Transformation to Foundry 4.0 |
||
|
|||||
12:00 |
Franco Bonollo |
Padova University, Dept. of Engineering and Management (DTG) |
20 Years of Research Projects targeted to Zero Defect Manufacturing in Diecasting |
||
|
Tuesday 9 October 9:30 - 12:30
SPEAKER |
COMPANY |
TITLE OF PAPER |
|||
---|---|---|---|---|---|
9:30 |
Alessandro Lazzari |
PETROLVALVES SPA |
Finite element analysis of a thermoplastic chevron packing |
||
|
|||||
9:50 |
Alexey Babenko |
Truboprovod |
PASS/HYDROSYSTEM - new opportunities of multiphase flow simulation in piping networks |
||
|
|||||
10:10 |
Clovis R. Maliska Jr. |
ESSS |
Particle Multiphysics Simulation for the Oil & Gas Industry Using Rocky DEM and ANSYS |
||
|
|||||
10:30 |
Simone Bosotti |
PETROLVALVES SPA |
CFD simulation of multiphase flow with solid particles through a ball valve for de-cocking service |
||
|
|||||
10:50 |
Coffee Break Time |
||||
11:20 |
Alberto Clarich |
ESTECO SpA |
Optimization of Compressed Natural Gas transportation Vessel: Gasvessel project |
||
|
|||||
11:40 |
Alberto Tacconelli |
Aidro Hydraulics & 3D Printing |
Design for Additive Manufacturing in Hydraulics applications: A new technical mindset to innovative Fluid Power systems |
||
|
|||||
12:00 |
Nicolò Spiezia |
M3E & SAIPEM |
Machine Learning for the speed prediction of subsea trenching activities |
||
|
|||||
12:20 |
Leonid Korelstein |
Truboprovod |
Usage of derivative-free optimization in PASS/HYDROSYSTEM piping network flow analysis software |
||
|
Tuesday 9 October 9:30 - 13:00
SPEAKER |
COMPANY |
TITLE OF PAPER |
||||
---|---|---|---|---|---|---|
9:30 |
Fermo Maspero |
Fonderia Maspero srl |
The new challengies of the metallurgy 4.0 |
|||
|
||||||
9:50 |
Olivier Jaouen |
Transvalor S.A. |
Numerical simulation in steelmaking industry: from melted metal to finished product |
|||
|
||||||
10:10 |
Antoine Bally |
ABS Centre Métallurgique |
Simulation of soft reduction in billet caster; impact on the product |
|||
|
||||||
10:30 |
Viktor Pocajt |
Key to Metals |
The usage and integration of material data in the metal working industry |
|||
|
||||||
10:50 |
Coffee Break Time |
|||||
11:20 |
Riccardo Pelaccia |
University of Modena and Reggio Emilia |
A novel SLM H13 cooling insert for extrusion dies: experimental and numerical investigations |
|||
|
||||||
11:40 |
Federico Fracasso |
EnginSoft SpA |
CAE approach to cold forming processes: an efficient and cost-effective solution for product-process development |
|||
|
||||||
12:00 |
Giulio Gallo |
OMFA Inox Srl |
Simulating hot forging processes: moving from practical experience into new markets |
|||
|
||||||
12:20 |
Antoine Navarro |
Transvalor SA |
Main benefits of a global numerical approach on metal forming processes |
|||
|
Tuesday 9 October 14:30 - 17:30
SPEAKER |
COMPANY |
TITLE OF PAPER |
|||
---|---|---|---|---|---|
14:30 |
Gabriele Milanese |
University of Genoa, Mechanical Engineering, DIME department |
Development of an integrated design platform for general turbomachinery application |
||
|
|||||
14:50 |
Philippe Senn |
SUPSI - Department of Innovative Technologies (DTI) |
Design Optimisation of a Thermal Energy Storage System for a Laboratory Scale AA – CAES |
||
|
|||||
15:10 |
Daniele Agazzi |
Brembana & Rolle |
CFD analysis of the flow distribution in a Waste Heat Recovery Unit |
||
|
|||||
15:30 |
Coffee Break Time |
||||
16:00 |
Emanuel Pesatori |
Exergy SpA |
Turbomachinery for an advanced sCO2 cycle |
||
|
|||||
16:20 |
Tanmay Tamboli |
Eaton India Innovation Centre LLP |
Modified Lumped Modelling approach for simulation of electrical components in Switchgears |
||
|
|||||
16:40 |
Julien Halleguen |
Onet Technologies |
Numerical Simulation of Replacement Sequencing of Pipe Components |
||
|
Tuesday 9 October 14:30 - 17:30
SPEAKER |
COMPANY |
TITLE OF PAPER |
|||
---|---|---|---|---|---|
14:30 |
Chris Cowan |
Ozen Engineering, Inc. |
Physics Based Simulation Applications in the Semiconductor Industry |
||
|
|||||
14:50 |
Angelo Malvasi |
iLABS |
Sensor networks for monitoring and predictive maintenance applications of productive plants |
||
|
|||||
15:10 |
Manolo Venturin |
EnginSoft SpA |
Anomaly detection and remaining useful life (RUL) estimation methods in predictive maintenance |
||
|
|||||
15:40 |
Coffee Break Time |
||||
16:00 |
Walter Ferrarese |
Orchestra srl |
Edge computing on CLOUD architecture: how to make your products smarter by shifting from the big to the small data paradigm |
||
|
|||||
16:20 |
Ian McLuckie |
Advanced Integrated Engineering Solutions Ltd |
Solid modelling and hex meshing combined to form a new CAD and CAE standard |
||
|
|||||
16:40 |
Miklòs Màrton |
ViveLab Ergo Ltd. |
A new chapter in ergonomic simulation |
||
|
|||||
17:00 |
Luca Baglivo |
Trentino Sviluppo SpA, ProM Facility |
Simulation tools Importance in Additive Manufacturing Process(SLM) |
||
|